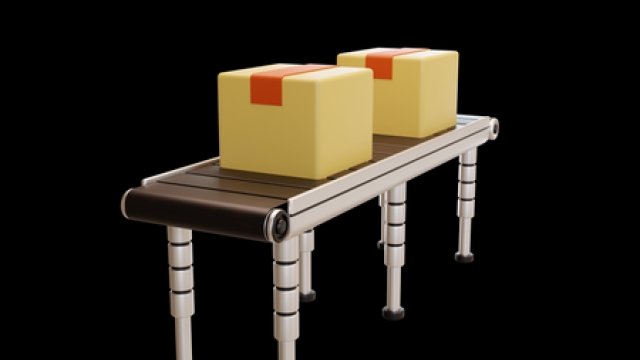
A Beginner’s Guide to Rubber Conveyor Belt Installation
Installing a conveyor belt can seem like a daunting task, especially for beginners. Whether you are dealing with rubber conveyor belts, PVC conveyor belts, or rubber drive belts, understanding the installation process is essential for ensuring smooth operation in various applications. This guide aims to simplify the installation journey, providing you with the necessary knowledge to effectively set up these vital components in your material handling systems.
As industries evolve, the design, development, and production of rubber conveyor belts have advanced significantly. These belts play a crucial role in enhancing efficiency and productivity in warehouses, manufacturing plants, and various other environments. By familiarizing yourself with the proper installation techniques and best practices, you can ensure that your conveyor systems operate at peak performance, minimizing downtime and maximizing throughput. Let’s dive into the key steps and considerations for installing rubber and PVC conveyor belts effectively.
Understanding Conveyor Belt Types
Conveyor belts are essential components in various industrial applications, facilitating the efficient transport of materials. The most common types of conveyor belts include rubber conveyor belts, PVC conveyor belts, and rubber drive belts, each designed for specific functions and environments. Understanding the characteristics of these belts is crucial for selecting the right one for your operations.
Rubber conveyor belts are known for their durability and flexibility, making them ideal for heavy-duty applications. They are commonly used in industries such as mining, agriculture, and manufacturing, where they can handle abrasive materials. Their robust construction allows them to withstand extreme temperatures and rough handling, ensuring long service life and reduced maintenance costs.
On the other hand, PVC conveyor belts offer unique advantages in terms of cleanliness and chemical resistance. These belts are often utilized in food processing and pharmaceuticals, where hygiene is critical. They are lightweight and easier to handle, making them suitable for lighter loads and environments that require frequent cleaning. Rubber drive belts play a different role, providing the necessary traction and power transmission in machinery. Understanding these differences will help you choose the right conveyor belt type for your specific needs.
Installation Best Practices
When installing rubber conveyor belts, it is crucial to ensure that the installation area is clean and free from debris. A clean environment minimizes the risk of contaminants that could affect the performance and longevity of the belt. Always inspect the conveyor system to identify any potential obstructions or damage that might hinder proper installation. Additionally, it’s important to have all necessary tools and components ready before beginning the process to facilitate a smoother installation.
Proper alignment of the conveyor belt is essential for optimal performance. Misalignment can lead to accelerated wear and tear, resulting in reduced efficiency and potential breakdowns. To achieve correct alignment, adjust the pulleys and rollers to ensure they are straight and level. Use a level to check the alignment periodically throughout the installation process, making adjustments as needed to maintain even tension across the belt. This attention to detail will help prolong the lifespan of both the belt and the entire conveyor system.
PVC Belt Manufacturers
Finally, after completing the installation, it’s recommended to conduct a thorough operational test of the conveyor system. Run the conveyor at various speeds and observe for any signs of slippage or unusual noises, which can indicate issues with the installation. Monitor the belt’s behavior closely during the first few hours of operation, and make any necessary adjustments. Following these best practices will help ensure a successful installation and enhance the performance of rubber and PVC conveyor belts as well as rubber drive belts.
Maintenance and Troubleshooting
Regular maintenance is essential for the longevity and efficiency of rubber conveyor belts, PVC conveyor belts, and rubber drive belts. Inspect the belts frequently for signs of wear, such as cracks, fraying, or surface damage. Keeping the belts clean and free of debris will help prevent any unnecessary strain on the system. Proper alignment and tension should be monitored as well; improper tension can lead to slippage and excessive wear, while misalignment can cause the belt to track incorrectly.
In case of any performance issues, it is important to troubleshoot the problem systematically. Start by checking the drive mechanism and ensuring that it is functioning properly. Next, examine the belt for foreign objects that may be causing blockages or damage. If the belt is not tracking correctly, adjusting the idler rollers or training the belt may be necessary. Identifying the root cause of any issues promptly will reduce downtime and improve the operational efficiency of the conveyor system.
If repairs are needed, follow the manufacturer’s guidelines for replacing or fixing sections of the belt. It is often more effective to replace defective belts entirely rather than attempting temporary fixes. Additionally, consider consulting with a professional for any major issues or for routine maintenance schedules. By adhering to regular maintenance and addressing problems quickly, you can ensure the reliability and effectiveness of your rubber and PVC conveyor systems.